Mold Image Analysis Technology for Maintaining AC Cleanliness: Remembering the Start of Kirei Check
Air conditioners now use a multitude of AI technologies. These technologies can be seen in a wide range of features, including a function that detects wall and floor temperatures in rooms, automatic operation that surveys past data for optimal operation and comfort, and predictive failure analysis based on big data. In addition to these, Daikin Industries has developed another new area for AI called Kirei Check. This service supports maintenance work by quickly evaluating the dirt and mold stains on existing air conditioners. In this interview, we spoke with the three engineers involved in development Kirei Check.
Interdisciplinary team from diverse backgrounds of chemistry, pharmaceutics, and optics
--Could you tell us about your education and work experience before and after joining Daikin?
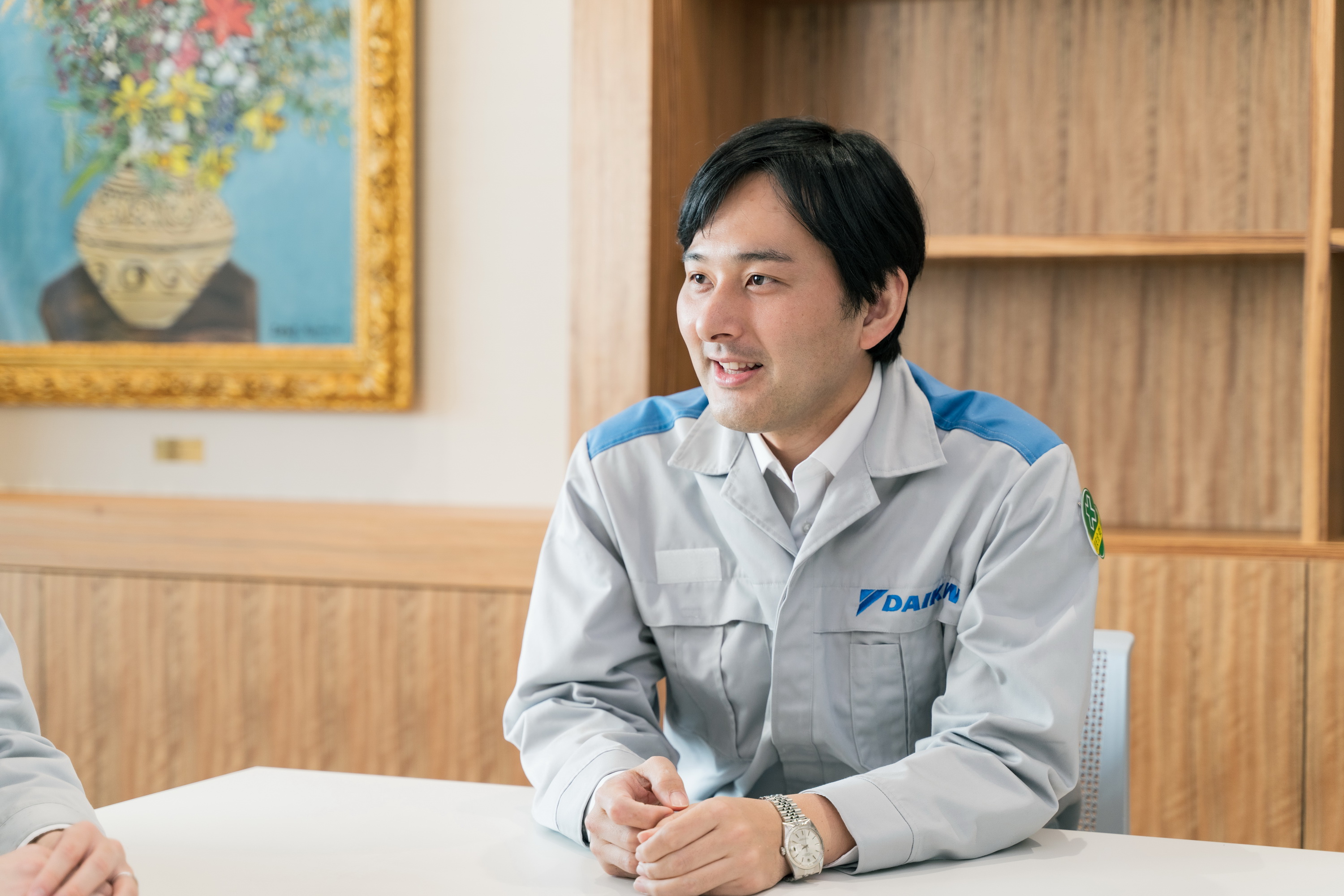
Namikawa: When I was a student at the Graduate School of Science, I measured the transfer rate of organic compounds irradiated by lasers and electron transfer. My specialty is organic chemistry and laser chemistry.
I am currently in my 17th year with the company and have been working in the Functional Materials Group of the Chemical Research and Development Center and the Product Research Department. Upon the establishment of the Technology and Innovation Center (TIC) in 2015, I was transferred to the New Functional Development Group, and in 2018, I became the leader of the Analytical Evaluation Technology Advancement Group as a senior engineer. In June 2022, I moved to the Chemical Advanced Technology Group, where I am currently working on the development of semiconductor materials and processes.
Maeda: After finishing university, I went on to graduate school in the faculty of pharmaceutical sciences, where I studied the function of enzymes involved in the survival of cancer cells at the microscopic level. I joined Daikin as a mechanical engineer and was assigned to TIC where I worked in the Analytical Evaluation Technology Advancement Group, led by Mr. Namikawa.
I was working on analysis of ventilation products and visualization of viable particles such as airborne viruses, pollen, and molds due to my background in pharmacy. I have been with the company for five years now, and in August 2022, I was transferred to the IAQ Technology Group, where I continue to be involved in the development of sensing technology for viable particles.
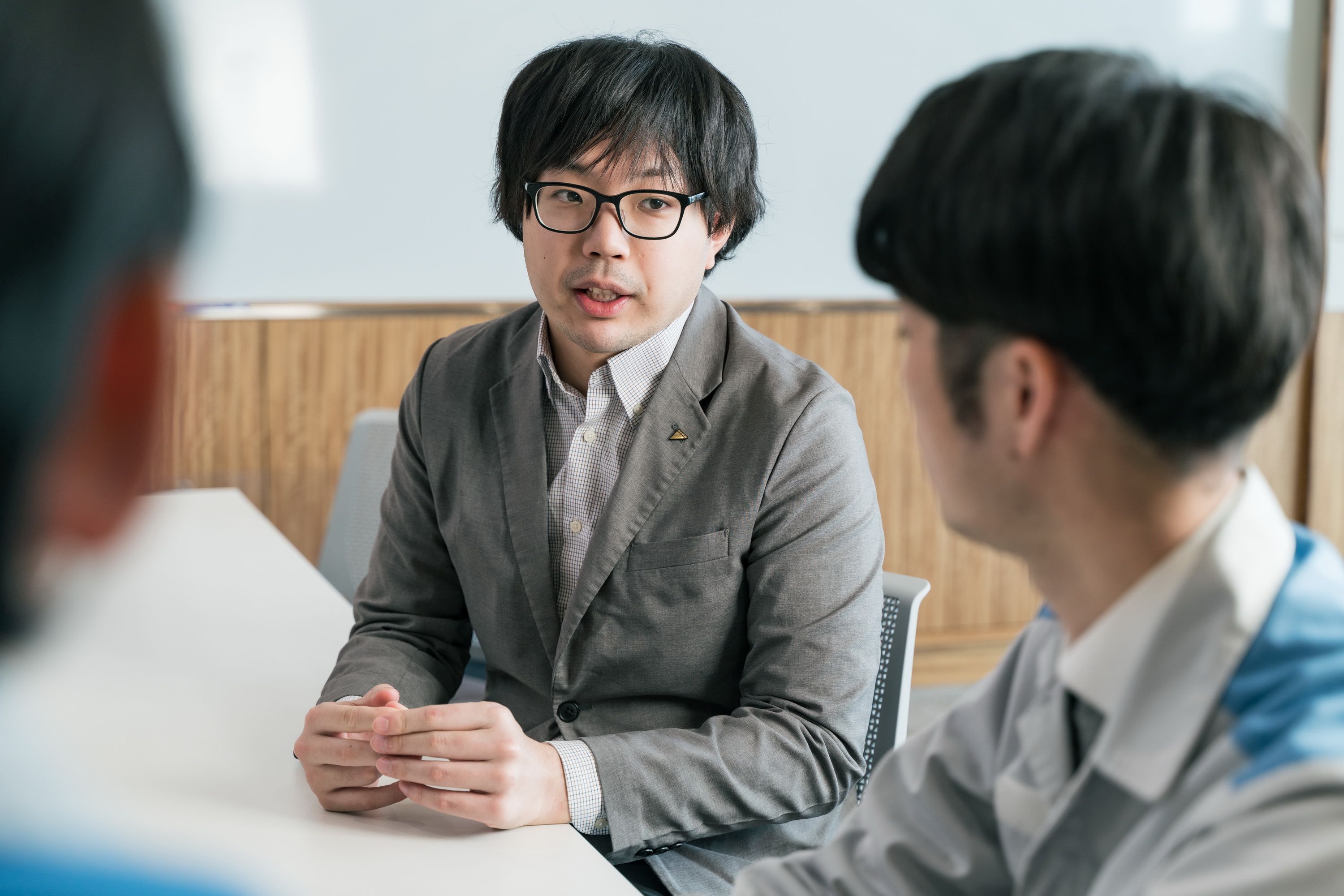
Kawai: I am 29 years old and have been with the company for five years. I was working on research to increase the intensity of X-rays at SPring-8 Angstrom Compact Free Electron Laser (SACLA), an X-ray laser facility located next to Super Photon Ring-8 GeV (SPring-8), a large synchrotron radiation facility.
After joining Daikin, I first entered the Daikin Information and Communications Technology College under the company's human resource development system and took AI courses for two years. Since FY2020, I’ve been assigned to the Analysis and Evaluation Technology Advancement Group at TIC, where I am mainly responsible for developing mold inspection tools, analyzing factory odors, and creating systems that correlate questionnaire sensory evaluations to AI.
New image analysis technology dramatically increases mold detection time and accuracy
--What inspired you to develop "Kirei Check" mold collection and analysis service?
Namikawa: While I was working on a different theme, I realized that each mold had a different shape and wondered if AI could be used to identify them. I proposed a new theme and started development on the theme of “identifying mold using AI” at the beginning of 2019. That was around the same time as the establishment of the Daikin Information and Communications Technology College.
Maeda : Mold thrives in damp, nutrient-rich areas. The rate of mold growth changes depending on room use and environment since mold favors wet areas where moisture tends to accumulate.
The After Sales Service Division, which is responsible for maintenance of existing air conditioners, had been providing mold sample collection and analysis services for years. However, when we adopted the theme, analysis had been outsourced to an institute specializing in mold. Including the mold cultivation period, it took approximately four weeks to report the results to the customer, which was a problem. We thought that if AI could be used to test for mold on-site, then the results could be immediately reported to the customer.
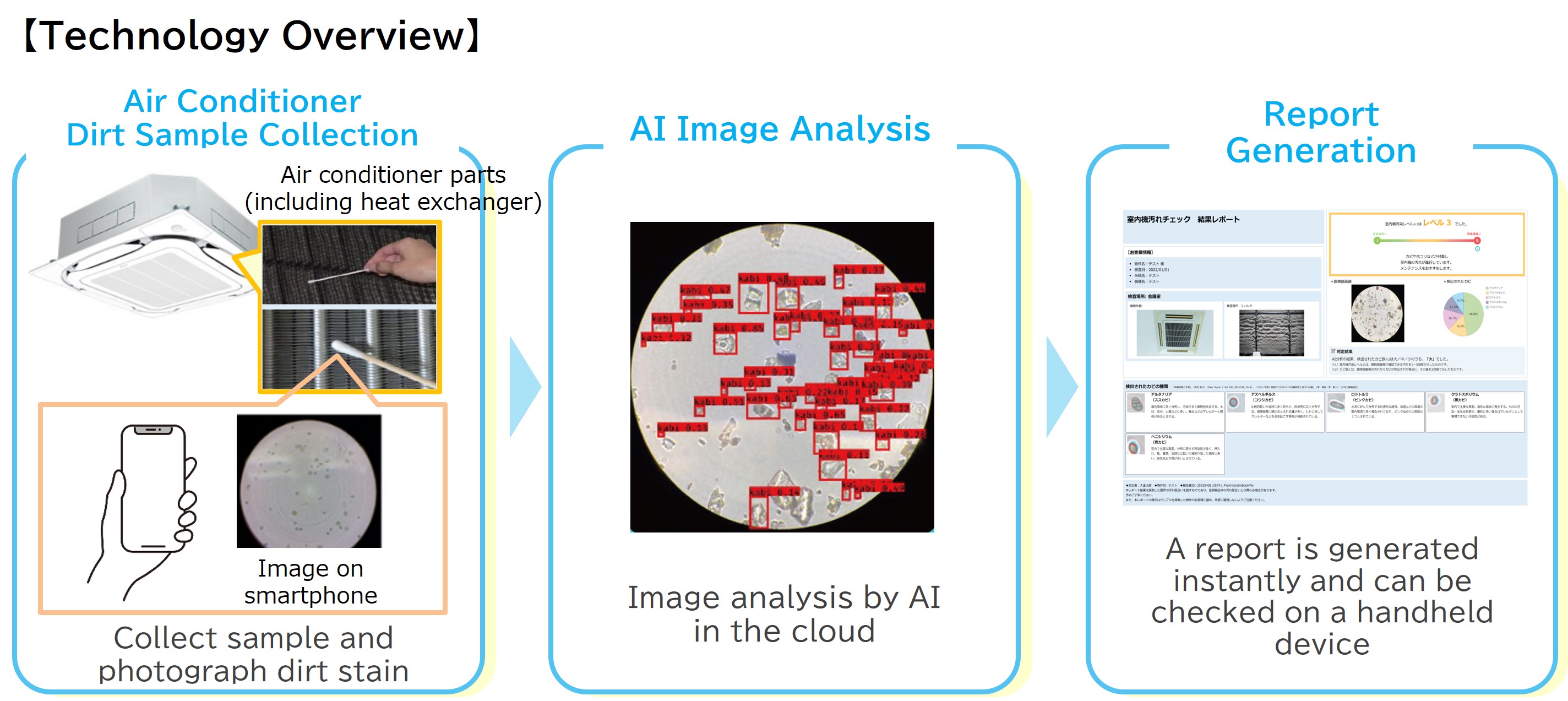
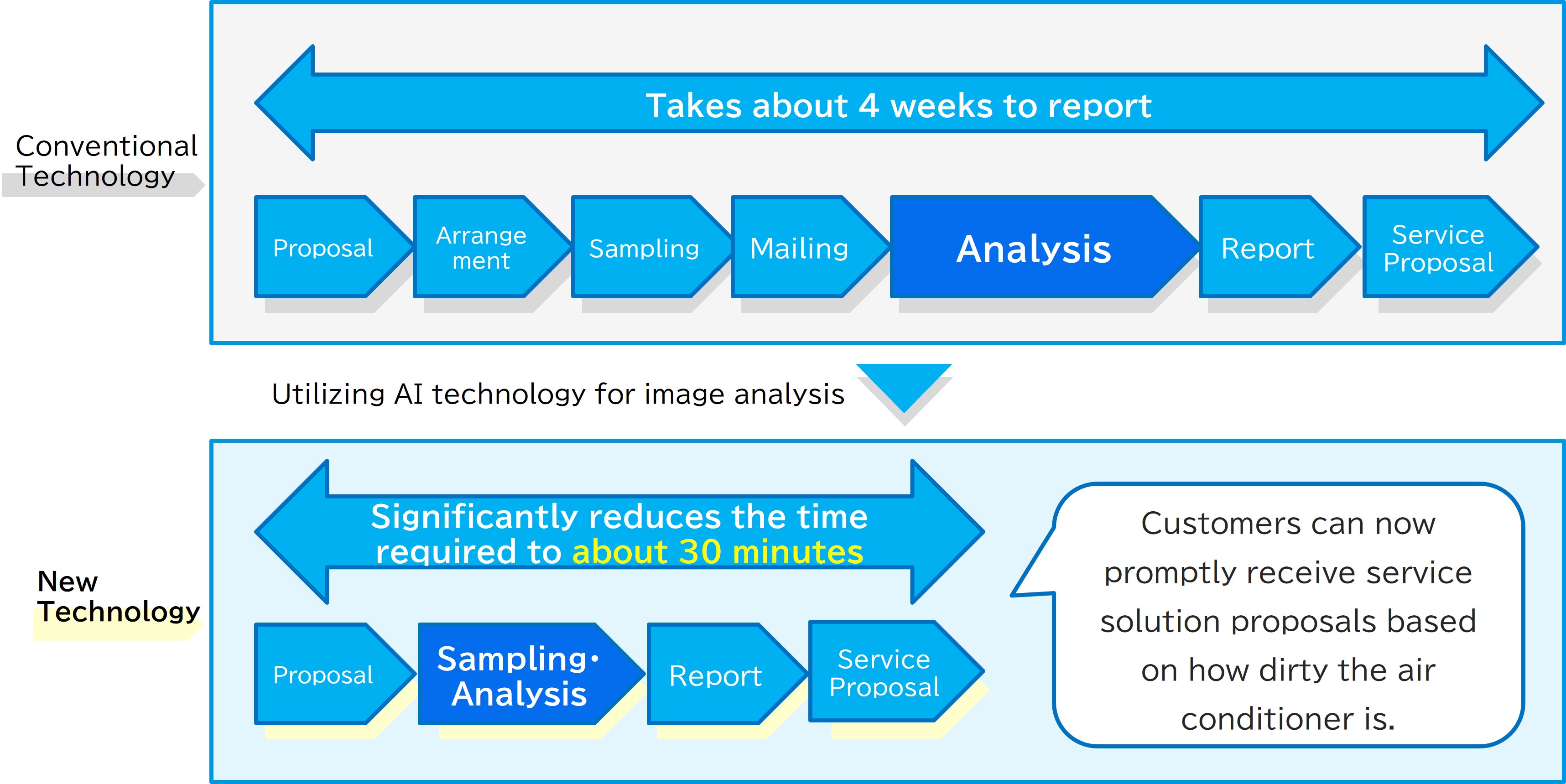
Microscopic images of mold collected from air conditioners can be captured with a smartphone and uploaded to the cloud. There AI is used to analyze and evaluate the mold, and a report is generated that can be viewed on-site.
This reduces the inspection period from approximately four weeks to 30 minutes, enabling timely customer proposals for service solutions tailored to the degree of mold contamination of the HVAC equipment.
Kawai: With Kirei Check, testing takes about 30 minutes from the time you collect the mold samples, take a picture of the mold with your smartphone, have it analyzed in the cloud, and receive a report on the results. If you just want to analyze mold, it takes less than a minute. By shortening the analysis time, results can be immediately communicated to customers when their interest is growing, which directly leads to opportunities to propose maintenance proposals, including cleaning of indoor units. In addition, the five levels of contamination can be displayed, so you can immediately check the condition of the air conditioner.
--What specifically is done to accurately determine mold in such a short time?
Kawai:
We were able to improve the accuracy of mold analysis by utilizing two types of AI. First, we combined an AI that identifies the location of mold inside an image with an AI that identifies mold.
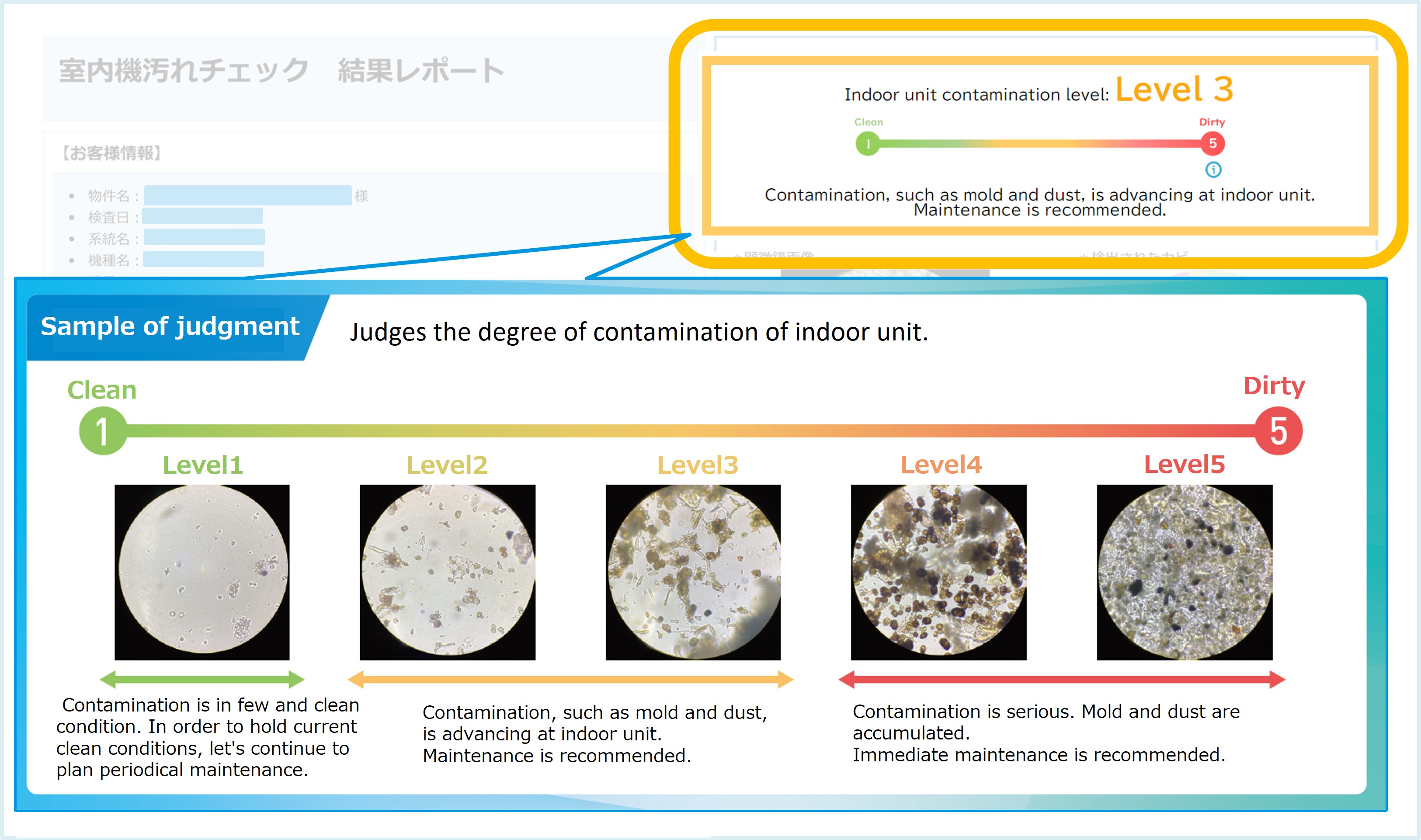
Below is an image of an actual indoor unit dirt stain check. The report also provides a 5-level stain evaluation that can be used to indicate appropriate maintenance.
Expanding opportunities for customer proposals with a free collection and analysis service
--What solutions do you propose for the results of mold stain analysis?
Namikawa: Filters and coating agents are proposed according to the level of dirt based on the cleaning of indoor units. I think it is a major point that our service engineers, who are air conditioning professionals, can propose in-house maintenance while examining the analysis results.
In our previous mold sampling and analysis service, customers had to pay the cost of analysis by an outside institute. However, many customers would hesitate to pay for this service without knowing that the dirt stain was contaminated with mold. In this respect, Kirei Check uses its own AI system as a free analysis service to drastically reduce costs. This is one of the reasons why customers are interested in Kirei Check: they think, "If it's free of charge, I'll have it done.” I think Daikin now has more opportunities to say, "Let's aim for a clean space together.”
--What kind of feedback have you received from customers?
Maeda: Until now, we have been showing pictures of the dirt stains inside the air conditioner, but by conducting the Kirei Check, we are now able to give customers a visual image of the extent of dirt and mold hidden inside. Customer comments include, “I’ve have been cleaning the filter regularly but never realized how dirty it really was,” and “Compared to just looking at it, Kirei Check is much more persuasive.”
Connecting with others is a catalyst for overcoming difficulties
--Did you have any turning points in product development other than technical aspects?
Namikawa: I started this project alone at first. It was still not very precise, but in order to create an image of how it should take shape and could be used, I visited the After Sales Service headquarters in Osaka once every two months to share progress. Eventually, the manager in charge at the After Sales Service headquarters took over, and I thought, “What happens if no one is interested?” but he saw the potential in the project and thought it was interesting. The After Sales Service headquarters put me in charge of the project. Undoubtedly, the personal relationships that had been developed were the turning point.
Having this opportunity has made it much easier to conduct interviews, and I’ve gained considerable feedback from the field. The data is all available in the cloud, so we are able to receive substantial data of actual cases, which are more accurate. This has led to more people becoming interested in the project, and the cycle has become better and better. In the end, I was happy to receive the President's Award in 2022.
Maeda: This project was my first development experience. Not only was it difficult to figure out the technology, but knowing how to work with the After Sales Service headquarters and getting the service to the release stage was hard. There was no way to know whether it would be useful or not until people tried it on-site. We prepared videos, manuals, and training sessions. Even so, there were still some errors that came out of the field. Even though Kawai and I felt perplexed at times, I think we both experienced growth in our abilities through the project.
Involving others, both inside and outside the company, leads to a good product.
--What is your message to other developers and future colleagues who wish to do this type of work?
Kawai: Researchers often think only of theories and possibilities. While that is important, I think it is better to maintain a balance with actual work. Only thinking on your own does not make things move, and to some that is almost the same as doing nothing. Doing one trial and error, even if it is a failure, is one less option on the road to success. If you neglect theory, you will not understand the reasons for failure, but if you only pursue theory to excess, you will not make any progress.
Maeda: I think it is important to involve the people around you and accomplish things as a team since teamwork provides the capability to pioneer what is difficult for one person to achieve alone. When I was a student, I was often given assignments to perform on my own, but this limited me to things that were an extension of what I could already do. Conveying the theme that you want to work on is important for involving people around you and working as a team. I hope everyone will keep that in mind.
Namikawa: I would like to speak from the perspective of technological development and people. First of all, it is important to be aware how the technical theme before you will be used after its completion. Even if you create good technology, you will become discouraged if people don’t use it, and your efforts will not lead to results. With this technology, we are aware of “who will be pleased” and “what will please them,” and I believe that the outcome of recognizing and solving problems in advance is what leads to results.
Also, establishing bonds with people is really important when you join a company. The speed of this project greatly accelerated through the building of a network of people within the company who listened and reached out to me when I needed help. It is also important to make connections with people outside the company. For example, this time we dealt with mold, but we did not have a mold expert in the company. Then I remembered that I talked with someone from a mold analysis institute about the properties of mold, and we had become friends. In this way, I believe that maintaining good relationships with people inside and outside the company led to good results for this project.
Takashi Namikawa
Chief Engineer, Technology and Innovation Center
Born in Osaka and joined the company in April 2006. He is in charge of advanced chemical technology development.
“I want to continue to take on the challenge of developing new technologies and new materials and processes in the environmental and semiconductor fields and deliver new value to the world through the power of chemistry.”
Shotaro Maeda
Technology and Innovation Center
Born in Hyogo Prefecture and joined the company in April 2018. He is responsible for air environment visualization technology.
“I would like to challenge the technology to visualize the ‘invisible’ air that always exists around us and bring peace of mind to people's lives.”
Shogo Kawai
Technology and Innovation Center
Born in Osaka and joined the company in April 2018. He is in charge of AI technology.
“I want us to provide comfortable air all over the world by combining AI technology with air conditioner technology. To achieve this, we continue to learn about the two technologies on a daily basis.”
Related article