Sudden Inspiration Appears after Much Agonizing: Toy Leads to Unique Idea for New Motor Evaluation Method
Inspiration for innovative ideas can often leap unexpectedly from the most unlikely of places, a phenomenon Michihiro Nakagawa knows all too well. In his fourth year with the company, Mr. Nakagawa and his colleagues were seconded to a national project called the Technology Research Association of Magnetic Materials for High-Efficiency Motors (MagHEM). Here he was tasked with creating a new method to directly measure energy loss (iron loss) in motors, which had typically been measured indirectly. After untold hours of agonizing over which direction to pursue, he had a sudden inspiration from a popular children’s toy.
Passion for research of self-position estimation system in autonomous driving
--What kind of research did you do as a student, and why did you choose to work for Daikin Industries?
Nakagawa: When I was in college, I researched the technology behind the self-position estimation systems used in both global positioning systems (GPS) and inertial navigation systems (INS) for application to agricultural machinery. That was the area in which I earned my master's degree. I joined Daikin Industries in 2009 because I always wanted to join a local company in my region. Although it was just after the Lehman Shock, I felt no hesitation since Daikin had impressed me as being strong and resilient enough to weather such environmental changes.
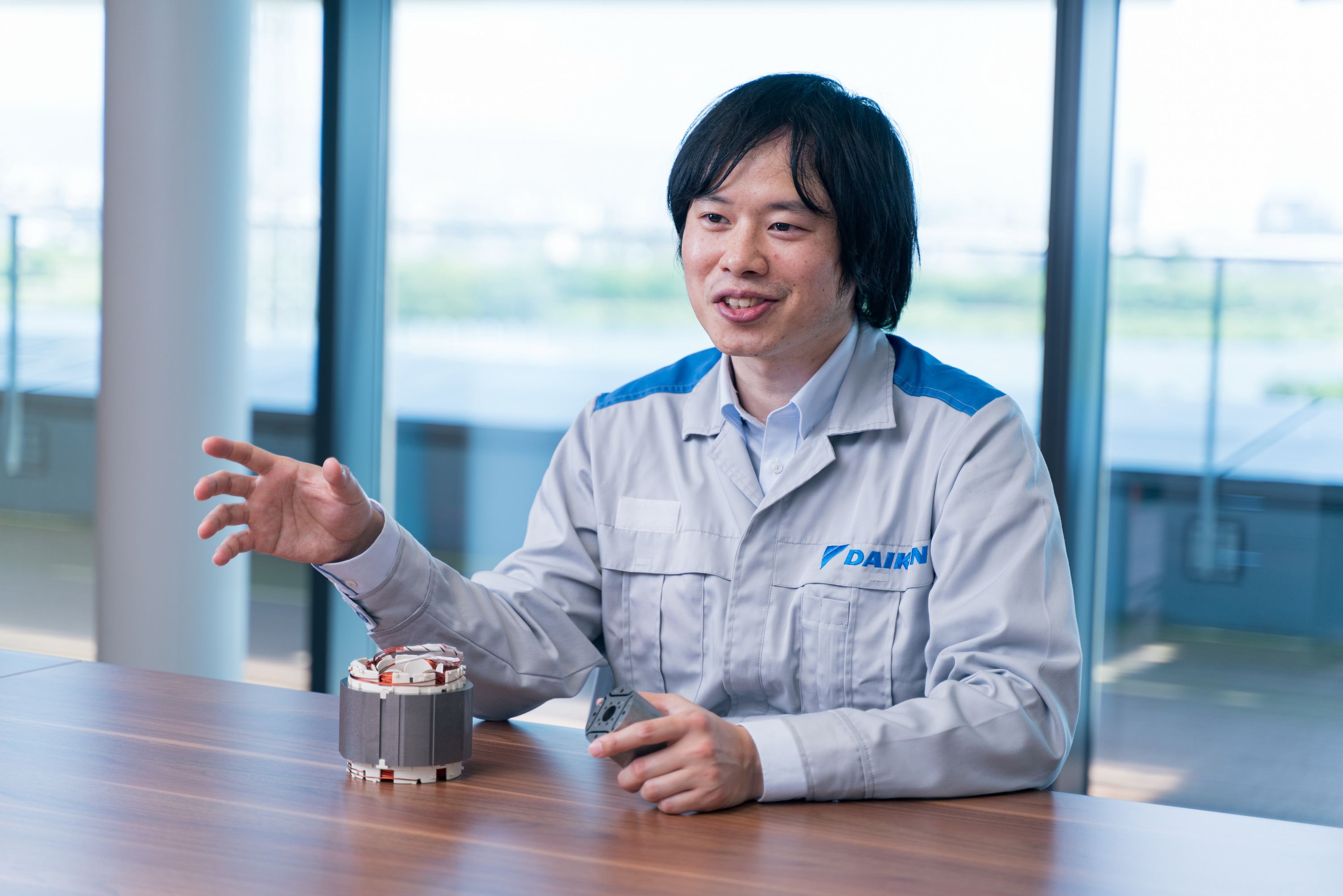
--How has your career advanced since joining the company?
Nakagawa: I was first assigned to the Environmental Technology Laboratory at Shiga Plant, where I started with research on reducing motor loss by developing inverter control methods. However, since the field had little to do with my university research, I had to learn it all from scratch, which was difficult.
Selected as a member of a government R&D project in fourth year with company
--You were involved in a government research and development project (hereafter referred to as the "national project") until this year.
Nakagawa:Yes, in 2012, I was seconded to the Technology Research Association of Magnetic Materials for High-Efficiency Motors (MagHEM), where I worked for about 10 years. Actually, I was far from being enthusiastic about it at first, but I gradually began to feel that I could do various things within the project. The theme of my research was development of new magnetic materials along with the design and development of motors for which the developed magnetic materials would be used. The aim was to achieve even higher energy efficiency targeting motors mainly for EVs, home appliances, and industrial use. I think I was chosen as a project member because the inverter research that I studied at Daikin Industries matched a theme of the national project.
--Could you provide some specifics about the project that you were involved with.
Nakagawa: Along with our company, members included the Osaka Prefecture University, which developed the world's first "reluctance motor" (IPMSM motor: a hybrid synchronous motor utilizing the power of both magnetic and reluctance torque) in collaboration with Daikin, and the Nagoya Institute of Technology (NIT), which has expertise in "variable-magnetic-force (VMF) motors" that change magnetic flux according to operating conditions. Originally, there had been five members from Daikin, including myself, but the number fell to three halfway through the project. Our mission was to "accurately evaluate and analyze high-efficiency motors designed by the university."
Development of the world’s first motor test equipment with a magnetic bearing for direct measurement of motor iron loss
--That mission is the reason you developed the world's first magnetic bearing motor loss analysis test equipment, isn’t it? Why did you adopt a magnetic bearing for the device?
Nakagawa: This test equipment was mainly developed and designed by the same members of the seconded team. The reason for adopting magnetic bearings was to improve the accuracy of motor loss measurement, and my responsibility was to measure and evaluate the motor loss using that equipment when the motor was operating.
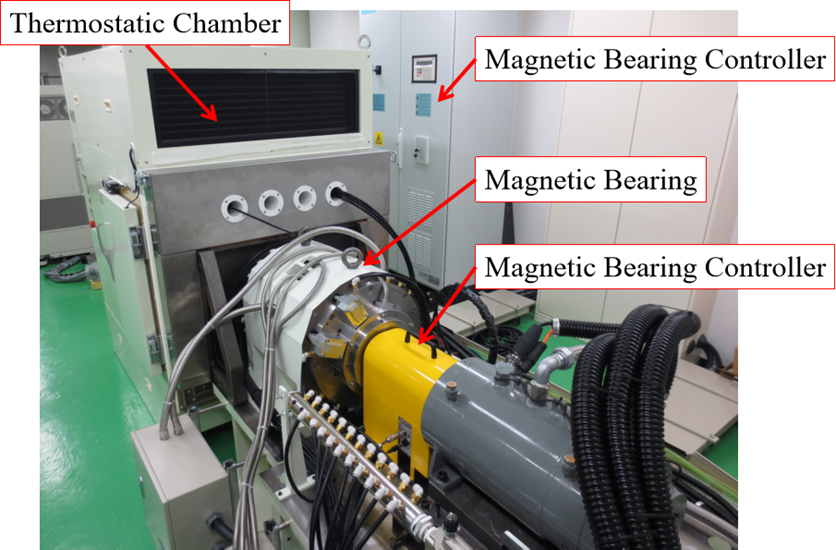
External view of the motor loss analysis and evaluation device developed by Daikin as a national project. Using magnetic bearings to reduce mechanical loss to near zero is the key point.
Conventional loss tests indirectly measure iron loss, which corresponds to the energy loss that occurs when the motor is magnetized. In other words, iron loss = motor input - motor output - copper loss - mechanical loss (bearing friction loss). That is the method for indirect estimation based on the energy input-output relationship. However, since the mechanical loss cannot be accurately measured during operation, a provisional value measured before operation is used. Nevertheless, since the mechanical loss varies each time, the indirectly measured iron loss value cannot be reproduced. Use of a magnetic bearing in the test equipment to float the shaft prevents mechanical loss from occurring.
Inspiration comes from the "Pop-up Pirate" game after much agonizing
--The measurement and evaluation method you developed, Mr. Nakagawa, was unique in that it directly measures iron loss, rather than indirectly. How did you come up with the idea?
Nakagawa: My own role was to relatively evaluate whether the iron loss measured by the motor loss analysis and evaluation device that we had developed was really the correct value. This is where I came up with the idea of measuring the B-H curve (magnetic hysteresis curve) by drilling a hole in the motor's stator and embedding an H coil (magnetic sensor) to directly determine iron loss.
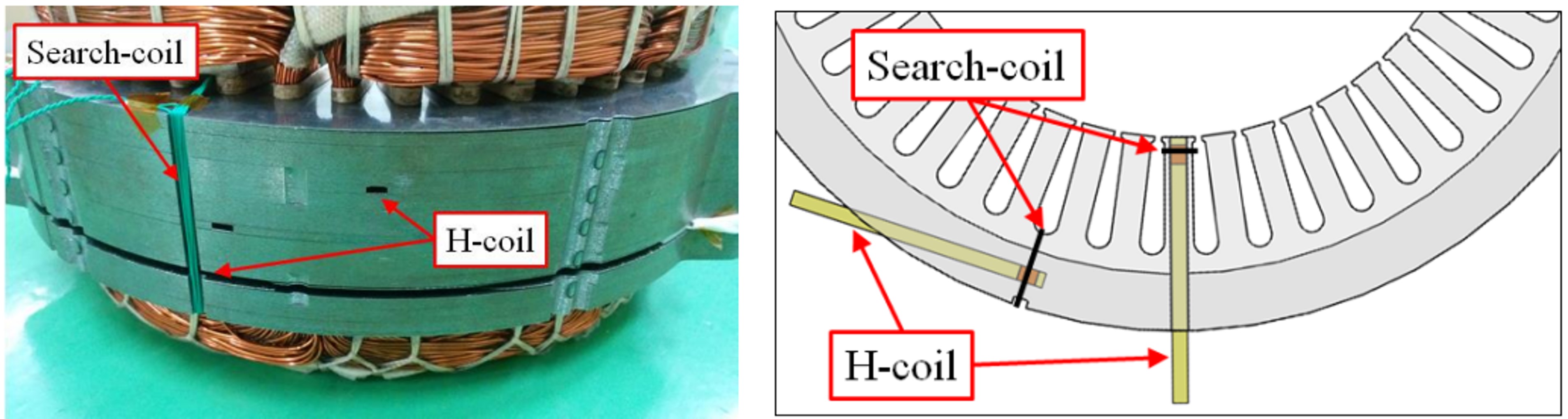
This measurement method was inspired by the Pop-up Pirate game. The measurement points were analyzed by magnetic simulation, and a hole was made in the motor's stator core for inserting an H coil.
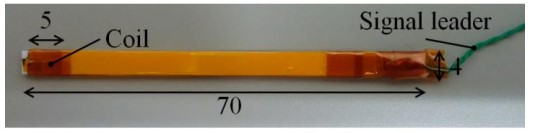
HExternal view of the H coil. Since neither development speed nor cost was justified, Mr. Nakagawa purchased a winding machine and made the coil himself.
Actually, I wrestled with how to measure it, but one night while trying to sleep, I suddenly thought of the Pop-up Pirate (a toy in which swords are inserted into holes of a barrel containing a bearded pirate). The barrel in the game corresponds to the stator of a motor, and the H coil is inserted into it like a sword. There have been measurement methods using H coils in the past, but they were used to investigate material properties and have rarely been applied to motors. This is because when an H coil is placed in a motor, the magnetic flux leaks from the air gap between the rotor and stator, making it difficult to measure properly.
--How were you able to properly measure iron loss??
Nakagawa: The exact B-H (magnetic flux density and magnetic field) is measured by embedding an H coil in the stator, and the area enclosed by the B-H (hysteresis loop) corresponds to the iron loss. When the experimental values from the magnetic bearing test rig correlate with the direct measurement of the iron loss evaluation, the results can be deemed correct. The advantage of this method is that we can visually see the change in iron loss and actually understand the increase in iron loss directly.
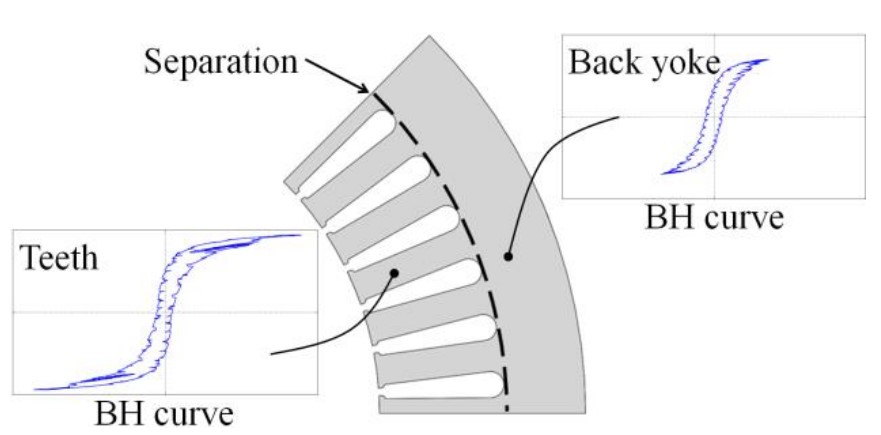
B-H (magnetic flux density - magnetic field) curve at each point. The area surrounded by this B-H corresponds to the iron loss. The sum of each point was used as iron loss.
High hurdles are ultimately overcome with the “give it a try” spirit
--What were some of the obstacles that you struggled to overcome and caused you the greatest amount of concern?
Nakagawa:All things considered, drilling a hole in the stator and inserting the H coil was the hardest part. The development period for this was during my fourth or fifth year of involvement with the national project. We thought that the conventional H coil method of measurement could not be applied directly to motors, so we took steps to solidify our basic research using a ring coil that generates an ideal magnetic field, and then applied it to motors.
Every day, I struggled with how to accurately measure iron loss in motors, and then one day the image of the Pop-up Pirate came to mind. It seemed insane to drill a hole in the stator in the first place, and I did it half out of desperation. (Laughs.) But the plan was to develop a technology to directly measure iron loss in motors, and there was no turning back at that point.
--Did you ever have moment when you were excited, and you knew that you had done it?
Nakagawa:The most memorable moment for me came when I was able to get the B-H in the motor exactly right. That's all I can really think of.
--Do you feel your work style is influenced by the Daikin corporate culture and spirit?
Nakagawa: Daikin has a spirit of challenge that says, "Let's first try to do everything possible.” Inserting the H coil into the stator was difficult, but we managed to find an EDM company that could process it, and they used a special jig to hollow it out. Here it is important to develop peripheral elemental technologies.
In the spirit of "try to do everything possible," I made the H coil myself. If I had asked the manufacturer, it would have taken about three months for delivery, and the cost would have been no less than 500,000 yen. It was not worth the time and cost required for development, so I decided to buy a winding machine and make the coils myself! (Laughs). It took a lot of time and effort, but we were able to verify the accuracy and produce results.
Freely involve those around you and be determined to persevere even when you hit a wall
-- Are there any areas for reflection on your 10-year involvement in a national project?
Nakagawa: The first good thing was that we were able to carefully spend time developing a new measurement method in a national project. I’m the type of person who agonizes over each detail, so I suffered greatly until the idea for the Pop-Up Pirate came to me. Upon reflection, if I had received the opinions and advice of others earlier on, instead of keeping it all to myself, I might have more easily come up with the idea without any anguish. I now know that it is really important to involve others. My only regret is that I did not get as far in the end with implementing a specific way for lowering iron loss.
--Finally, do have any advice or comments for other developers and junior colleagues?
Nakagawa:I guess my advice is to never give up even if you are struggling with something and stuck in development. When you hit a wall, I think it is important to think tenaciously. During my research, I never had the attitude of giving up. Since it was a national project, a certain amount of the national budget was being used, and so we felt a lot of pressure with a large burden on us. I was very happy and a bit relieved that we were able to produce results.
Michihiro Nakagawa
Technology and Innovation Center
Joined the company in April 2009. Born in Osaka Prefecture.
Being responsible for the development of motor control technology.
I aim to reduce the losses of all motors related to Daikin products and contribute to solving energy issues worldwide. I continue to tackle technical challenges diligently every day.
Related article