Environment
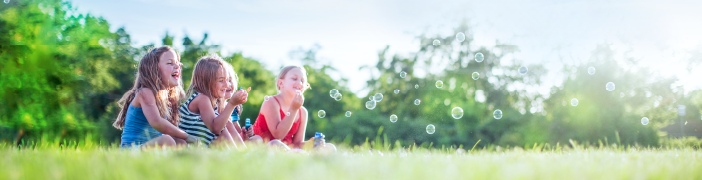
Daikin’s mainstay air conditioners consume large amounts of electricity during usage. As the world’s only manufacturer of both air conditioners and refrigerants, Daikin is working to reduce environmental impacts throughout the entire product life cycle.
Environment (Sustainability Report 2024) (3.3MB)
Main Reporting Items
- Environmental Management
- Response to Climate Change
- Challenge to Achieve Carbon Neutrality
- Initiatives for a Circular Economy
- Protecting Biodiversity
- Water Resource Conservation / Management and Reduction of Emissions and Chemical Substances
Related information
Data (Sustainability Report 2024) (2.1MB)
Main Reporting Items
- ESG Data
- Third-Party Verification
- Basic Environmental Policy
- Environmental Policy of the Daikin Group in Japan
- Basic Policy of Protecting Biodiversity
- Product Safety Voluntary Action Guidelines
- Product Assessment Items