Daikin’s Micro-Hydroelectric Power Generation System: First business created by TIC shows full range of Daikin
Micro-hydroelectric power generation systems with an output of less than 100 kW are eco-friendly devices that effectively harness kinetic energy from small rivers and streams, irrigation systems, sand dams, and water and sewer systems. However, until now, application had been especially limited since the amount of power generation had consistently failed to justify system cost and size. To address these issues, Daikin leveraged its expertise in the development of inverters and motors in the air conditioning and oil hydraulic businesses to successfully commercialize the new technology. Curious to learn more, we spoke with Mr. Atsushi Suhara, the TIC technical development leader involved in the micro-hydroelectric power generation system.
Realizing the importance of renewable energy and need for micro-hydroelectric power
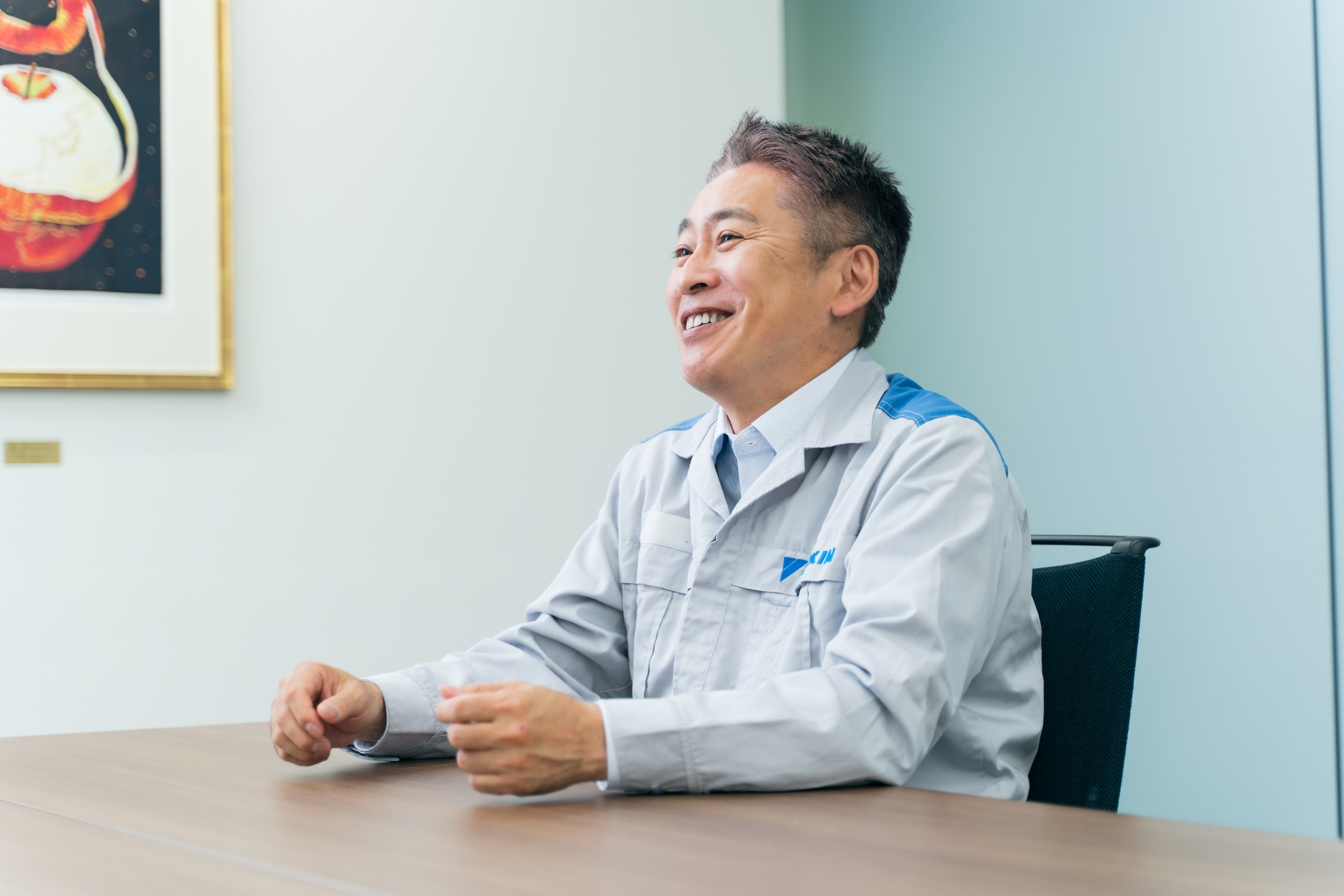
――Could you explain briefly about your background and Daikin work history?
Suhara : Surprisingly,
in my university days, I performed lab research on artificial bones, so my situation
was a bit unconventional since many people join Daikin to focus on motor and
inverter research. But because Daikin had a Medical Engineering (ME) department
dedicated to developing devices, such as blood glucose level monitors and immunoassay
measurement instruments, I looked forward to working in the medical field.
In 1994, I was assigned to the Electronics
Technology Laboratory where I initially worked on the development of automatic
transmissions for large trucks and was in charge of control software. Later, I
also worked on a joint project between the laboratory and the Oil Hydraulics Division,
where we developed a hybrid pump system using both motors and hydraulic drive
for energy-efficient pumps used in machine tools and molding machines. I was
also involved in the development of hybrid drive systems for power shovels,
which had an engine-driven generator mechanism. These experiences eventually
led to my involvement in the development of micro-hydroelectric power
generation systems.
――How did you become involved in micro-hydroelectric power generation systems?
Suhara: Since entering the company, I have always been involved in the development of products other than air conditioners. In 2011, the Great East Japan Earthquake occurred, and energy became a concern to society. This prompted me to reassess my contribution to the company and society. While solar and wind power rely on natural conditions that can be unstable, I turned my attention to hydroelectric power generation, which can provide stable energy regardless of the time or weather.
In fiscal year 2013, we applied for the Ministry of the Environment's “Enhanced Inducement-Type Technology Development and Demonstration Project for Reducing CO2 Emissions.” Our project was selected, marking the development start of micro-hydroelectric power generation systems with an output of less than 100 kW. Over the course of three years in this project, we developed two micro-hydroelectric power generation systems, each with different capacities, and conducted demonstrations in two different regions.
System development, including demonstrations, in a short three-year period
――What challenges did you face in developing micro-hydroelectric power generation systems?
Suhara:First, as a target for micro-hydroelectric power generation systems, we focused on the pipelines in waterworks facilities. These pipelines are internal pipes filled with water, and since the flowing water does not come into contact with air in these pipelines, we could expect significant power generation output based on the pipe pressure and water flow. Unfortunately, with no prior experience in developing low government projects, we lacked knowledge of waterworks and facilities. This became our initial hurdle. We proposed a concept of developing a low-cost, space-saving system while collecting public information from waterworks providers and conducting on-site interviews.
My own responsibility was in control software, whereas the mechanical aspects were handled by members from the Oil Hydraulics Division. Naturally, none of us had experience with turbines, so we began by gaining knowledge of turbine operation along with their energy efficiency and characteristics. We concurrently developed performance testing equipment to investigate these aspects. However, the installation conditions at waterworks facilities varied in terms of flow rate and drop height, and operations also differed subtly. Therefore, we had to consider how to meet these different requirements and accomplish the project, including design, manufacturing, demonstration testing, and equipment removal, within a short three-year period. It was a truly challenging situation at the time.
――What system did you develop specifically?
Suhara: We developed a micro-hydroelectric power generation system designed to maximize the utilization of untapped energy in the pipelines of waterworks facilities. The overall system consists of a highly efficient variable-speed (permanent magnet synchronous) generator, a vertical inline pump reverse turbine, and a power generation controller, among other components. The power generation controller is integrated with the generator to minimize installation space and achieve cost-effective solutions for both deployment and maintenance. Furthermore, we utilized the motor and inverter technology that Daikin had developed over the years in the fields of air conditioning and hydraulic equipment to achieve high efficiency.
Our goal was to create an economically efficient system that maximizes power generation while minimizing installation space, deployment costs, and maintenance expenses.
In principle, the system operates by harnessing the power of water flow in a pipeline to rotate a turbine. The shaft of the turbine is connected to the generator via a coupling, which converts the rotational energy of the generator into alternating electrical energy. This energy is then transformed into direct current using the power generation controller (converter). Furthermore, it is converted back into alternating current using a grid-connectable inverter within the system control panel, making it usable as a commercial power source.
Cost reduction strategies for practical use and demonstration of selling mechanism
――What are the key features of Daikin’s micro-hydroelectric power generation system?
Suhara: The biggest feature is its significantly lower cost compared to conventional systems. Substantial cost savings was achieved by using off-the-shelf components for a grid- connectable inverter that connects to the grid and by repurposing pumps to serve as the turbine. Initially, we designed custom runners, but they turned out to be cost-prohibitive, so we opted to use commercially available runners. Traditional turbines were typically custom-made, contributing to the high costs associated with hydroelectric power generation and being one of the reasons the system failed to gain wide acceptance.
The generator and control controller were integrated into a single unit, which was placed on top of the turbine, allowing us to minimize the installation footprint by configuring the system vertically and making it easier to install the system in tight spaces within existing waterworks facilities. We also devised a cooling mechanism to handle the heat generated by the system. Notably, we utilized the water from the waterworks facility itself for the water cooling mechanism.
Furthermore, conventional hydroelectric systems require complex mechanisms to maintain a constant rotation speed of the turbine, and guide vanes are used to adjust the flow rate. Our micro-hydroelectric power generation system utilizes motor and inverter technology to control flow while varying turbine speed. This allows us to convert previously wasted water energy into electricity and maximize the electrical output. Control software, which incorporates new functions to control flow and pressure, also plays a crucial role. Generator control follows the desired flow rates of the waterworks facility by applying reverse torque during regenerative operation.
For the demonstrations, we developed 22 kW and 75 kW hydroelectric systems and selected waterworks facilities in Minami-Tonami City, Toyama Prefecture, and Soma City, Fukushima Prefecture, as installation sites. Demonstration results confirmed sufficient power generation capacity and performance within the existing waterworks facilities with no disruptions to operations for trouble-free, stable power generation.
In Minami-Tonami City, Toyama Prefecture, a single 22 kW-class generator was installed, while in Soma City, Fukushima Prefecture, a combination of two 22 kW-class generators and one 75 kW-class generator was deployed.
The appearance of the micro-hydroelectric power generation system for pipelines is as follows: The 22 kW-class system (left) has dimensions of approximately 930 mm (width) x 546 mm (depth) x 1270 mm (height), with a pipe diameter of 150 mm. It weighs approximately 500 kg. The 75 kW-class system (right) measures about 1140 mm (width) x 637 mm (depth) x 1380 mm (height), with a pipe diameter of 200 mm. It also weighs approximately 500 kg. The system control panel is common to both systems and is compact with dimensions of approximately 1000 mm (width) x 800 mm (depth) x 1600 mm (height).
Following the development of this project, the TIC development team initiated a pilot project, and in 2017, DK-Power (※1) was established. DK-Power commercialized the 22 kW and 75 kW micro-hydroelectric power generation systems for pipelines and launched them in the market. As of the end of 2023, these systems have been adopted in 44 locations and 57 waterworks facilities across Japan.
※1. DK-Power
> https://www.dk-power.co.jp/
First TIC commercial venture returns part of electricity sales to water utilities
――What are your thoughts on the commercialization of the research and development project you worked on.
Suhara:Within Daikin, it has been quite rare for newly developed projects to lead to commercialization. Experiencing the entire process of “Can it truly be profitable, and can it become a viable business?” was extremely valuable to me.
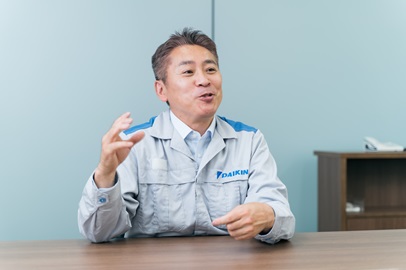
――Could you elaborate on the specific business application of the micro-hydroelectric power generation system.
Suhara: DK-Power is responsible for selecting pumps that meet the conditions of waterworks facilities, configuring the piping, and arranging local electrical contractors while promoting the implementation of micro-hydroelectric power generation systems in various regions. The basic scheme involves renting a location within a waterworks facility to install the power generation system, selling the generated electricity to the power company, and returning a portion of the income to the waterworks facility. It's similar to a vending machine business model.
Because securing reliable energy will continue to be a challenge in the future, I am delighted that micro-hydroelectric power generation can contribute to addressing this issue. I am also wondering the possibilities for introducing the system to various other waterworks facilities in the future. Since waterworks facilities are essentially universal, I believe that there will be a growing demand even in emerging countries where social infrastructure is being developed. Based on the domestic track record of this system, I hope to eventually promote global adoption and contribute to decarbonization.
――Looking back, what can you say about the culture and environment of conducting research at TIC?
Suhara: TIC has an environment where skilled professionals from various fields come together. Even when faced with something unknown, I can quickly seek the advice of an expert. My case may be unique in that I've also worked with colleagues outside of TIC, so I feel at ease consulting with people from other departments at TIC. In any case, Daikin has a culture where someone will always lend a helping hand when another colleague is confronting difficulties. I believe that effective communication with various people can make work progress more smoothly.
Atsushi Suhara
Technology and Innovation Center
Joined the company in April 1994 and is a native of Aichi Prefecture. He is responsible for the control software of micro-hydroelectric power generation and aims to contribute to achieving carbon neutrality by working on electric power generation projects using renewable energy.
Related article