What are the strengths of Daikin Industries' compressors and how have you overcome challenges in development?
Speaking of Daikin Industries' distinctive compressors, the first compressor we would like to introduce is the swing compressor. While other companies use rotary compressors in their residential air conditioner compressors, Daikin Industries is the only company that uses swing compressors. Daikin Industries also used to use rotary compressors. However, in accordance with the Montreal Protocol that went into effect in 1989, the refrigerant R22, which had been used in air conditioners until then, contained many ozone-depleting components, so the shift was made to HFCs, which caused a fatal problem with rotary compressors.
NEWS
Differentiating Technologies Support Daikin Compressors
FEATURE
2022.10.25
Compressors, the heart of air conditioning systems, account for 80-90% of the total power consumption of air conditioners. In anticipation of carbon neutrality by 2050, air conditioner manufacturers understand, more than ever, the importance of increasing compressor efficiency as an ongoing energy conservation measure. Behind Daikin Industries' continued No. 1 position in sales in the air conditioner industry is a strength in compressors that no other company has, a conceptual power to develop such compressors, and an ability to take action.
Chief Engineer Hideki Matsuura of the Technology and Innovation Center, who has led development of compressor technology at Daikin for many years, talks about the strengths of Daikin's compressors and the development capabilities that support them.
Chief Engineer Hideki Matsuura of the Technology and Innovation Center, who has led development of compressor technology at Daikin for many years, talks about the strengths of Daikin's compressors and the development capabilities that support them.
Swing compressors, conceived for refrigerant compatibility
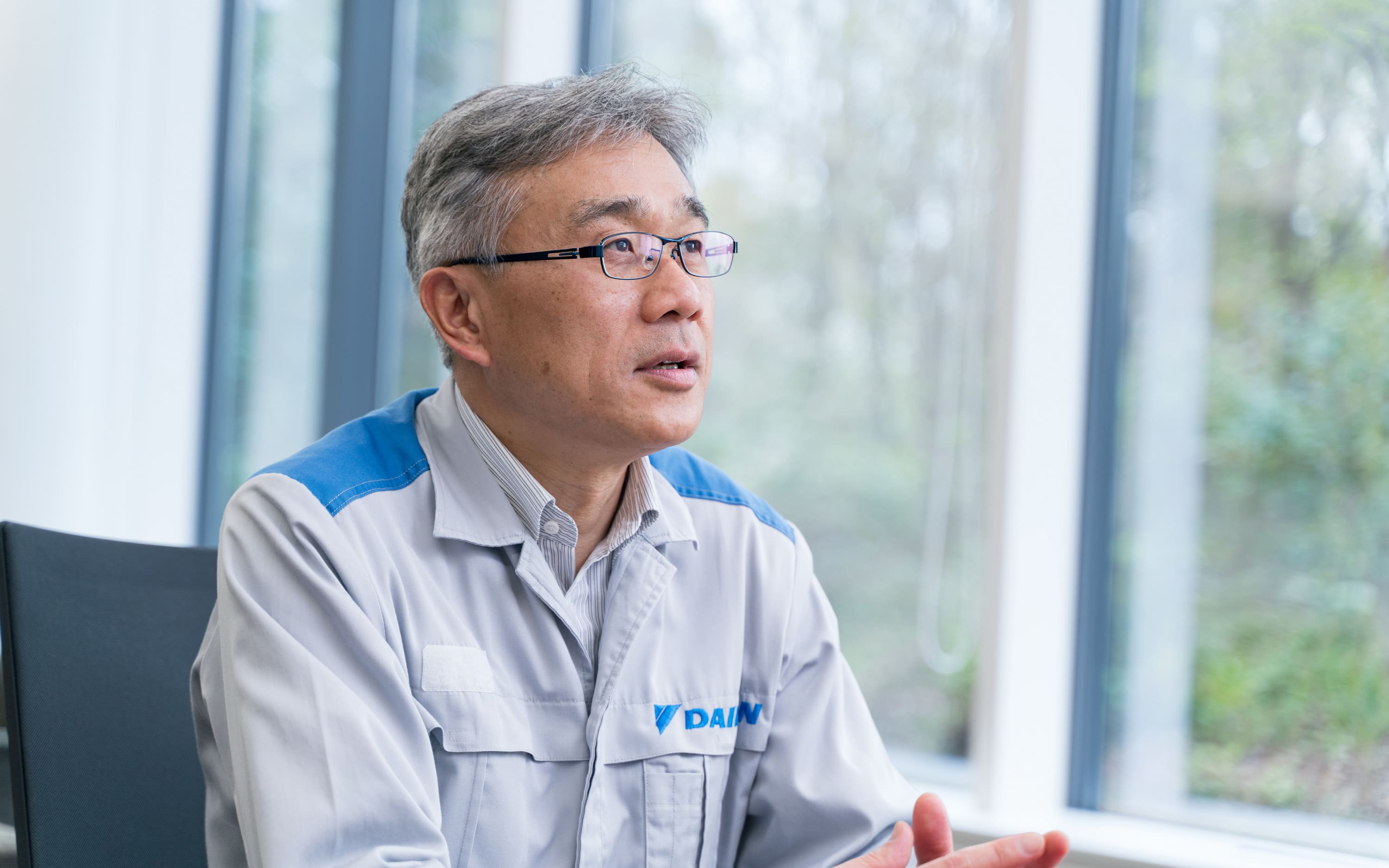
R22 is a refrigerant that contains chlorine, a substance not found in HFC refrigerants. The loss of chlorine made lubricating the vane tips more difficult, necessitating a review of the vane material and adjustment of the load on the spring that presses against the roller (Fig. 1 [a]) and creating the perfect time to reexamine the product from a structural standpoint.
Daikin devised a solution to this lubrication problem by integrating vane and roller into a single unit (Fig. 1 [b]). This revolutionary structure not only eliminates the need to worry about wear of the vanes and rollers by eliminating the need for springs, but it also prevents leakage from the part separating the intake and discharge chambers.
Daikin devised a solution to this lubrication problem by integrating vane and roller into a single unit (Fig. 1 [b]). This revolutionary structure not only eliminates the need to worry about wear of the vanes and rollers by eliminating the need for springs, but it also prevents leakage from the part separating the intake and discharge chambers.
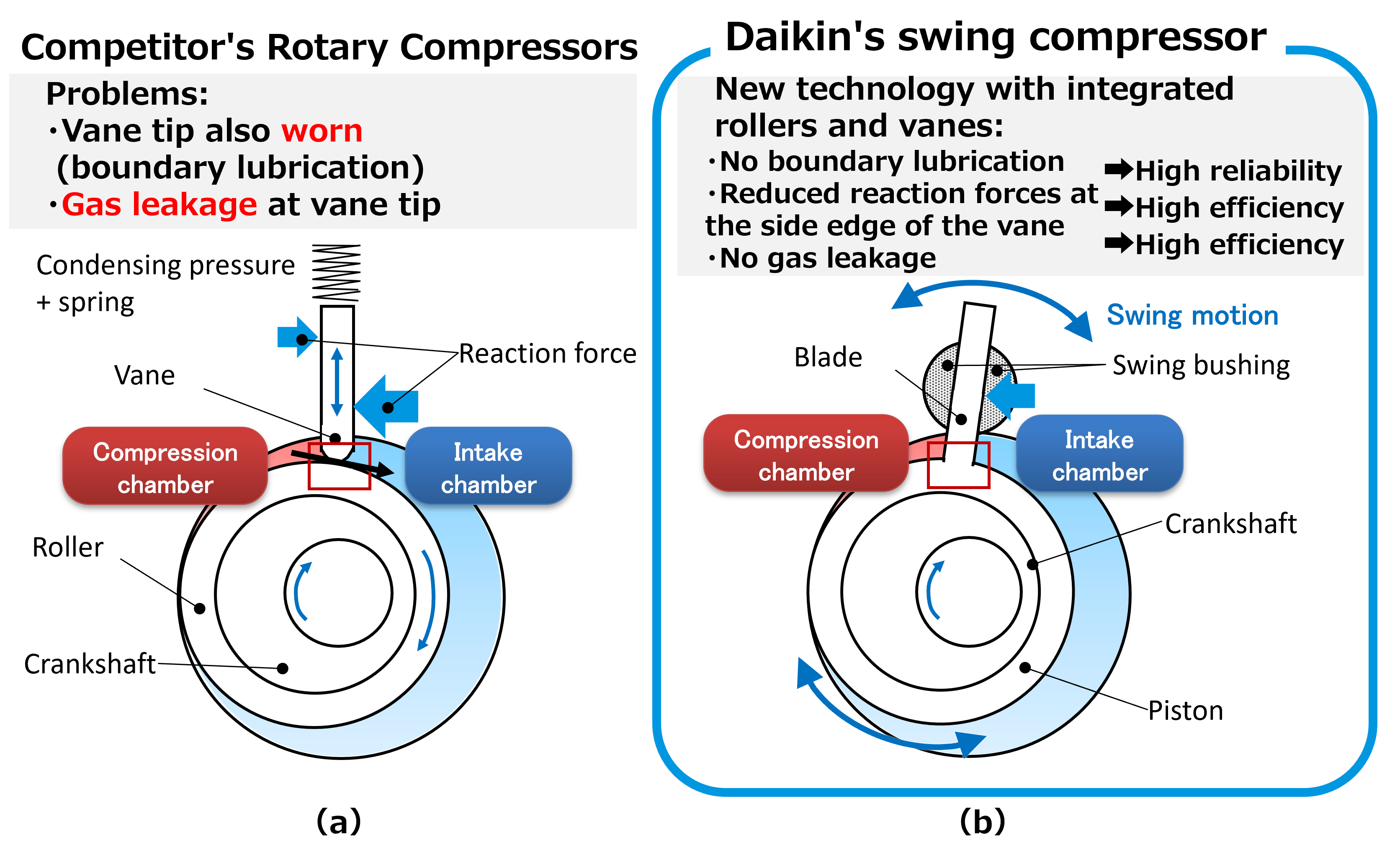
A "leak-proof" compressor is especially effective at low rotation speeds. In a rotary compressor, performance sharply drops at low speeds below 10 revolutions per second due to leakage caused by the loss of vane movement following. In contrast, Daikin swing compressors exhibit only a nominal drop in performance even at speeds as low as 4 revolutions per second.
The piston, which integrates vane and roller, swing up, down, left, and right as it rotates, and a new component called a swing bushing is used to support it. As long as the piston is in motion, the piston and swing bushing are constantly sliding against each other. In Figure 1(b), the swing bushing and piston appear to be in surface contact, but in reality they are in linear contact at the base of the vane.
Although there had been concerns about wear since line contact is more prone to wear on the contact surface than on the surface contact, theoretical studies and experiments confirm that wear from oil film formation on the contact point is not a problem. This fact led to a decision on the material for the sliding part, and we were able to commercialize the product.
However, swing compressors with low leakage have a manufacturing disadvantage in that machining accuracy of the piston is poor relative to cylindrical parts such as rollers. We succeeded in improving the accuracy by applying a cutting and polishing process suitable for machining the complex shapes where the vanes and rollers are integrated.
The piston, which integrates vane and roller, swing up, down, left, and right as it rotates, and a new component called a swing bushing is used to support it. As long as the piston is in motion, the piston and swing bushing are constantly sliding against each other. In Figure 1(b), the swing bushing and piston appear to be in surface contact, but in reality they are in linear contact at the base of the vane.
Although there had been concerns about wear since line contact is more prone to wear on the contact surface than on the surface contact, theoretical studies and experiments confirm that wear from oil film formation on the contact point is not a problem. This fact led to a decision on the material for the sliding part, and we were able to commercialize the product.
However, swing compressors with low leakage have a manufacturing disadvantage in that machining accuracy of the piston is poor relative to cylindrical parts such as rollers. We succeeded in improving the accuracy by applying a cutting and polishing process suitable for machining the complex shapes where the vanes and rollers are integrated.
Daikin expertise extends beyond swing compressors
Besides compressors utilizing the swing structure, Daikin Industries boosts a compressor lineup of scroll, single-screw, and centrifugal compressors. All of these compressors incorporate Daikin's unique technologies.
Scroll compressor
The scroll is composed of a structure in which two spiral-shaped scrolls mesh and rotate to change volume and compress the refrigerant. The orbiting scroll rotates while being pressed against the fixed scroll, and the contact area is lubricated with oil to prevent wear.
Scroll compressors from other manufacturers use refrigerant pressure to press the orbiting scroll against the compressor, but changes in refrigerant pressure due to operating conditions can result in increased leakage and sliding loss. Daikin reduces frictional losses in sliding parts by applying suitable pressure to the orbiting scrolls and using a new grooved structure between each scroll to promote oil lubrication. This has resulted in a 20% reduction in mechanical loss and a 2-point improvement in compression efficiency compared to conventional models.
Scroll compressors from other manufacturers use refrigerant pressure to press the orbiting scroll against the compressor, but changes in refrigerant pressure due to operating conditions can result in increased leakage and sliding loss. Daikin reduces frictional losses in sliding parts by applying suitable pressure to the orbiting scrolls and using a new grooved structure between each scroll to promote oil lubrication. This has resulted in a 20% reduction in mechanical loss and a 2-point improvement in compression efficiency compared to conventional models.
Single screw
Screw compressors are generally twin-screw compressors in which the male and female rotor screws mesh together, but Daikin Industries has a unique structure in which a resin gate rotor is sandwiched between a single screw. Compared to twin screws, the Daikin compressor is easier to balance against the shaft and achieves higher efficiency because it requires less bearing load.
Centrifugal compressor
Daikin's unique technology for controlling magnetic circuits has eliminated rolling bearings in favor of a magnetic bearing structure that uses magnetism to float the shaft. Bearings need to be lubricated with oil to prevent seizure, but magnetic bearings do not require lubricating oil. This not only eliminates the need for oil and cooling systems to lubricate the bearings and for maintenance, but also offers the advantages of low noise, low vibration, and high efficiency.
Daikin compressors for the right application at the right capacity
Four types of compressors of different construction are used for different applications and capacities: swing, scroll, screw, and centrifugal compressors. Swing is used for residential and retail applications, which tend to operate at low speeds, followed by scroll for building and chiller applications, and screw and centrifugal for chiller applications (Refer to Figure 2).
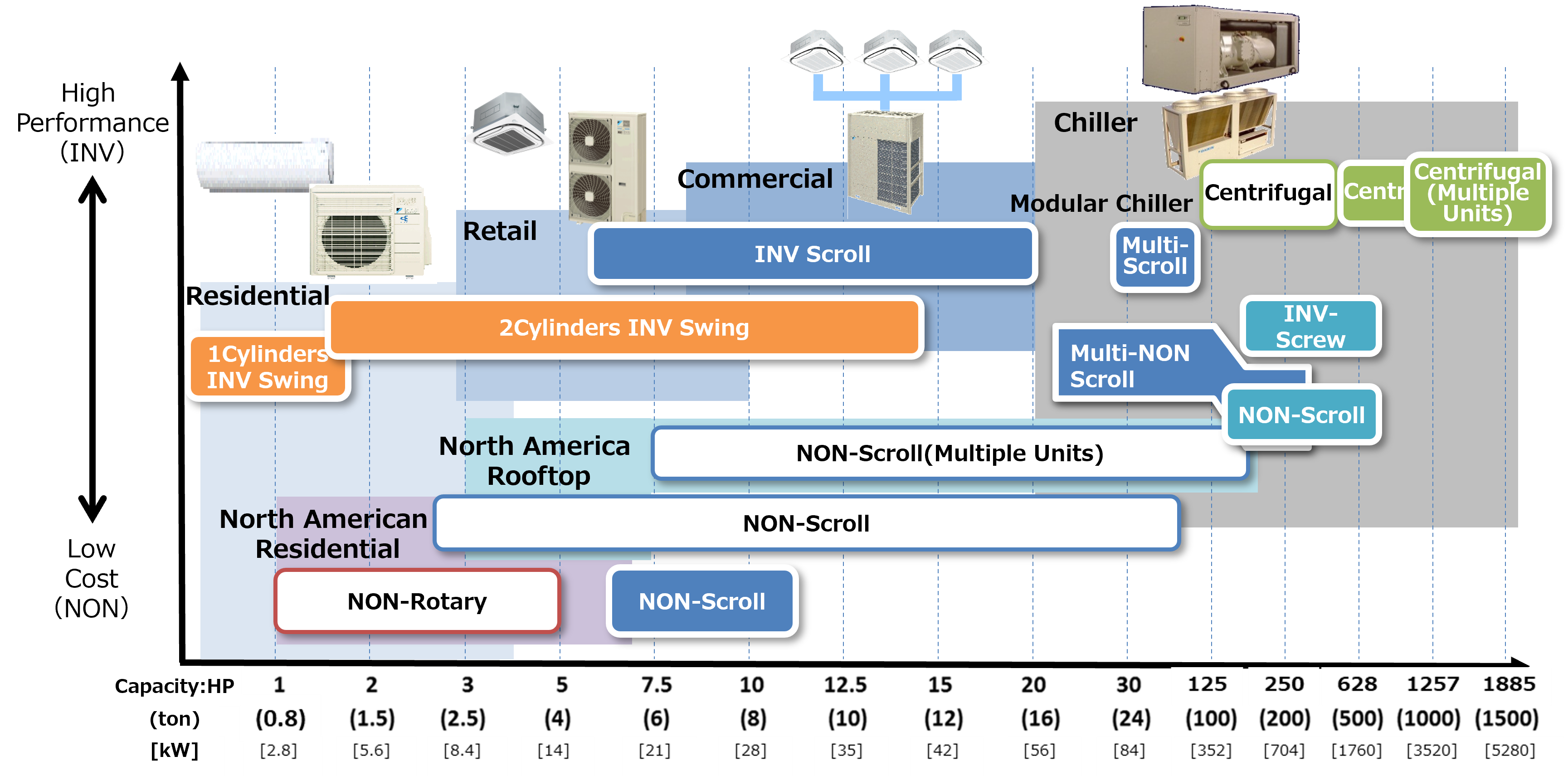
Each compressor also has different performance requirements. Compressors for homes and stores are often used at low speeds and require low-speed performance, and compressors for buildings require performance at the rated efficiency point. Swing compressors are effective at low speeds, whereas scroll, screw, and centrifugal compressors demonstrate good performance at the rated efficiency point.
The suitable compressor also depends on the refrigerant used. Centrifugal compressors and screw structures are suitable for low-pressure refrigerants such as 134a, while swing and scroll compressors are suitable for high-pressure refrigerants such as R410A and R32.
The suitable compressor also depends on the refrigerant used. Centrifugal compressors and screw structures are suitable for low-pressure refrigerants such as 134a, while swing and scroll compressors are suitable for high-pressure refrigerants such as R410A and R32.
Support for further miniaturization
In addition to higher efficiency, miniaturization (resource conservation) is also a key development goal. Rather than globally supplying air conditioning equipment equipped with compressors designed for the Japanese market, Daikin develops compressors that conform to the needs of each region. For example, all air conditioners for India and Asia are cooling-only units for residential use. Local needs necessitated a reduction in manufacturing costs, and miniaturization of the swing compressor was essential (to reduce material costs). By rotating a small compressor at high rpm, we were able to reduce the weight by about 25% and improve the efficiency by 1 point compared to the rotary compressors of other overseas competitors.
Miniaturizing a swing-type compressor presented many challenges. The smaller the size, the smaller the compression volume per revolution, so the rotation speed was increased. However, increasing the rotation speed also tends to increase clogging in the discharge path, so we optimized the design of the valve opening timing and opening/closing speed.
Also, increasing the rotational speed causes louder noise and greater vibration due to unbalance, so we reviewed the design to improve noise and vibration. The final product was commercialized with a rotation speed that was 1.5 times higher than that of the previous model.
The need for downsizing is not limited to swing compressors. In light of future material price hikes, such as for electrical steel sheets and copper, we must continue conserving resources. We are also working on downsizing in scroll, screw, and centrifugal compressors.
Miniaturizing a swing-type compressor presented many challenges. The smaller the size, the smaller the compression volume per revolution, so the rotation speed was increased. However, increasing the rotation speed also tends to increase clogging in the discharge path, so we optimized the design of the valve opening timing and opening/closing speed.
Also, increasing the rotational speed causes louder noise and greater vibration due to unbalance, so we reviewed the design to improve noise and vibration. The final product was commercialized with a rotation speed that was 1.5 times higher than that of the previous model.
The need for downsizing is not limited to swing compressors. In light of future material price hikes, such as for electrical steel sheets and copper, we must continue conserving resources. We are also working on downsizing in scroll, screw, and centrifugal compressors.
Will compressors change dramatically? Issues for refrigerant compatibility
The most difficult part of compressor development is that the refrigerant can change to comply with refrigerant regulations.
In the 1990s, we eliminated the problem of ozone layer depletion caused by refrigerants containing chlorine, such as R22, by switching to R410A and R32 and have been optimizing designs to match refrigerant properties
In 2012, Daikin Industries became the first company to adopt R32, which has a low global warming potential (GWP), and it succeeded in both reducing the greenhouse gas emissions as required by the Kyoto Protocol and miniaturizing the compressor. Over the past 10 years, we have increased our ratio of air conditioners and chillers utilizing R32 refrigerant to 50%.
In contrast, it has recently become necessary to further reduce global warming potential. EU refrigerant regulations are most advanced in the world, and the amount of HFCs (※) sold in the EU market is being regulated in stages. By 2030, we will no longer be able to sell air conditioners containing HFCs, and it will be necessary to switch to refrigerants with a lower GWP than R32.
For example, R1234yf is a refrigerant used in automobile air conditioners and has a GWP of 10 or less. Since compressor capacity is one-third that of R32, the refrigeration system would not be viable unless the compression volume of the compressor were tripled. However, tripling the compressor volume is not realistic for commercialization because of the unavoidable cost increase. Increasing the rotational speed could be considered, but the hurdle is high in terms of mechanical reliability, such as bearing life.
In addition, refrigerant compatibility is not only a technical challenge. The timing of the refrigerant switchover can be delayed by as much as 10 years or more due to regional differences in regulations, making it necessary to increase the number of models to accommodate various refrigerants, which poses both development and production challenges.
Currently, we are in the process of developing technologies and production setups to solve these issues based on the collective wisdom of all parties involved.
*HFC: Hydrofluorocarbon is a refrigerant, such as R134a, R32, and R410A, that does not contain chlorine, and therefore does not deplete the ozone layer.
In the 1990s, we eliminated the problem of ozone layer depletion caused by refrigerants containing chlorine, such as R22, by switching to R410A and R32 and have been optimizing designs to match refrigerant properties
In 2012, Daikin Industries became the first company to adopt R32, which has a low global warming potential (GWP), and it succeeded in both reducing the greenhouse gas emissions as required by the Kyoto Protocol and miniaturizing the compressor. Over the past 10 years, we have increased our ratio of air conditioners and chillers utilizing R32 refrigerant to 50%.
In contrast, it has recently become necessary to further reduce global warming potential. EU refrigerant regulations are most advanced in the world, and the amount of HFCs (※) sold in the EU market is being regulated in stages. By 2030, we will no longer be able to sell air conditioners containing HFCs, and it will be necessary to switch to refrigerants with a lower GWP than R32.
For example, R1234yf is a refrigerant used in automobile air conditioners and has a GWP of 10 or less. Since compressor capacity is one-third that of R32, the refrigeration system would not be viable unless the compression volume of the compressor were tripled. However, tripling the compressor volume is not realistic for commercialization because of the unavoidable cost increase. Increasing the rotational speed could be considered, but the hurdle is high in terms of mechanical reliability, such as bearing life.
In addition, refrigerant compatibility is not only a technical challenge. The timing of the refrigerant switchover can be delayed by as much as 10 years or more due to regional differences in regulations, making it necessary to increase the number of models to accommodate various refrigerants, which poses both development and production challenges.
Currently, we are in the process of developing technologies and production setups to solve these issues based on the collective wisdom of all parties involved.
*HFC: Hydrofluorocarbon is a refrigerant, such as R134a, R32, and R410A, that does not contain chlorine, and therefore does not deplete the ozone layer.
Development capabilities behind Daikin compressors
Rather than academic research, Daikin Industries is promoting many developments with an eye toward mass production that can contribute to business in a year or two.
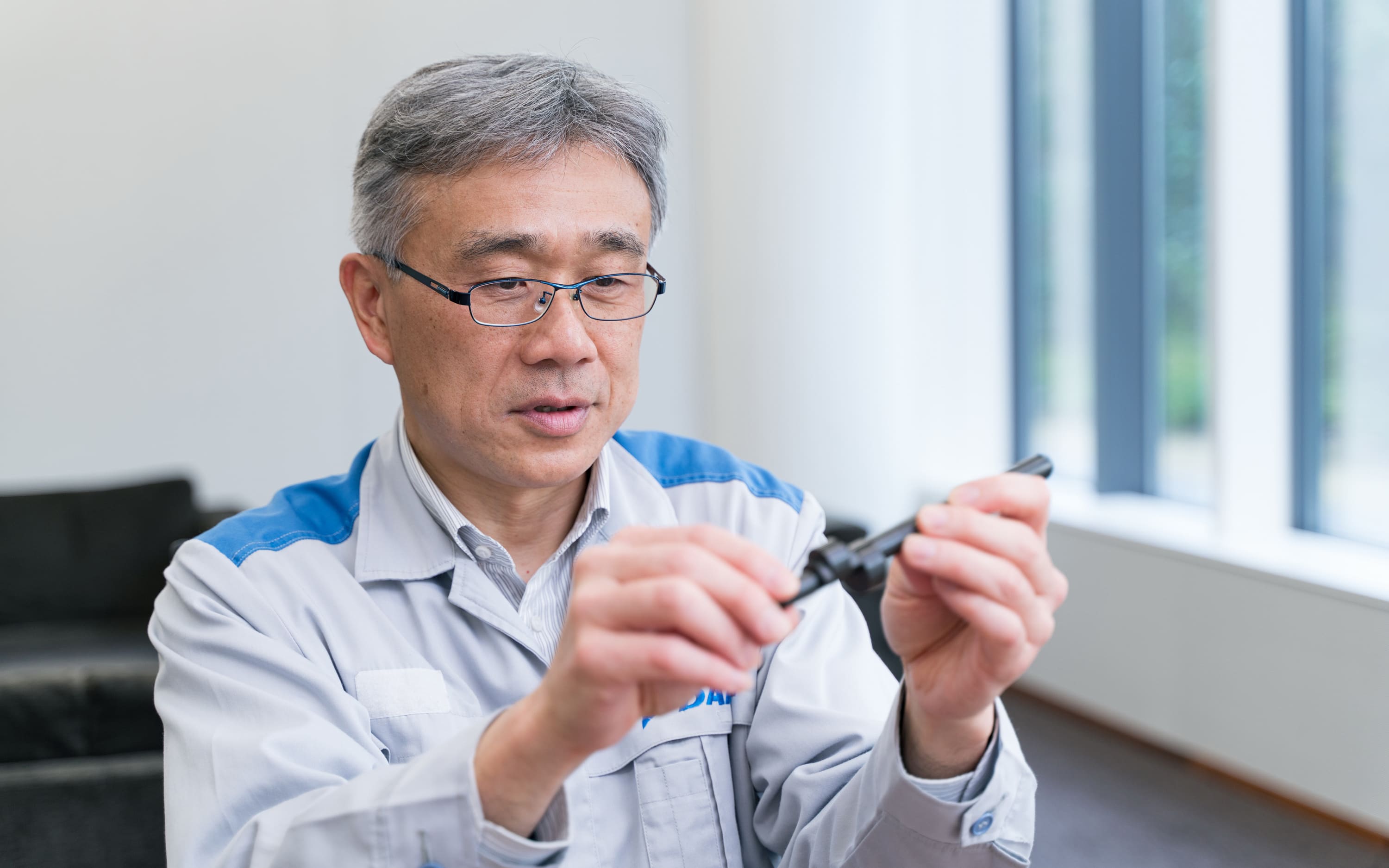
At the same time, we are also promoting development that looks several years or more into the future and goes beyond conventional compressor concepts. In order to create new compressors with high value, we are not only developing new technological seeds but also upgrading the design evaluation standards themselves and increasing development speed through frontloading. We are also actively engaged in fluid analysis, vibration, and sound field analysis. Although it is a challenge to establish analysis methods and validation methods, it is a rewarding workplace where we can overcome various technical challenges and contribute to the environment and our business.
Demand for air conditioners is expected to triple the current level by 2050. Daikin Industries will continue to expand production, but we will not be complacent with our No. 1 market share. We will continue to develop compressors that contribute to products that can be said to be "viable because they use Daikin compressors” and excel in technology, production, and profitability.
Demand for air conditioners is expected to triple the current level by 2050. Daikin Industries will continue to expand production, but we will not be complacent with our No. 1 market share. We will continue to develop compressors that contribute to products that can be said to be "viable because they use Daikin compressors” and excel in technology, production, and profitability.
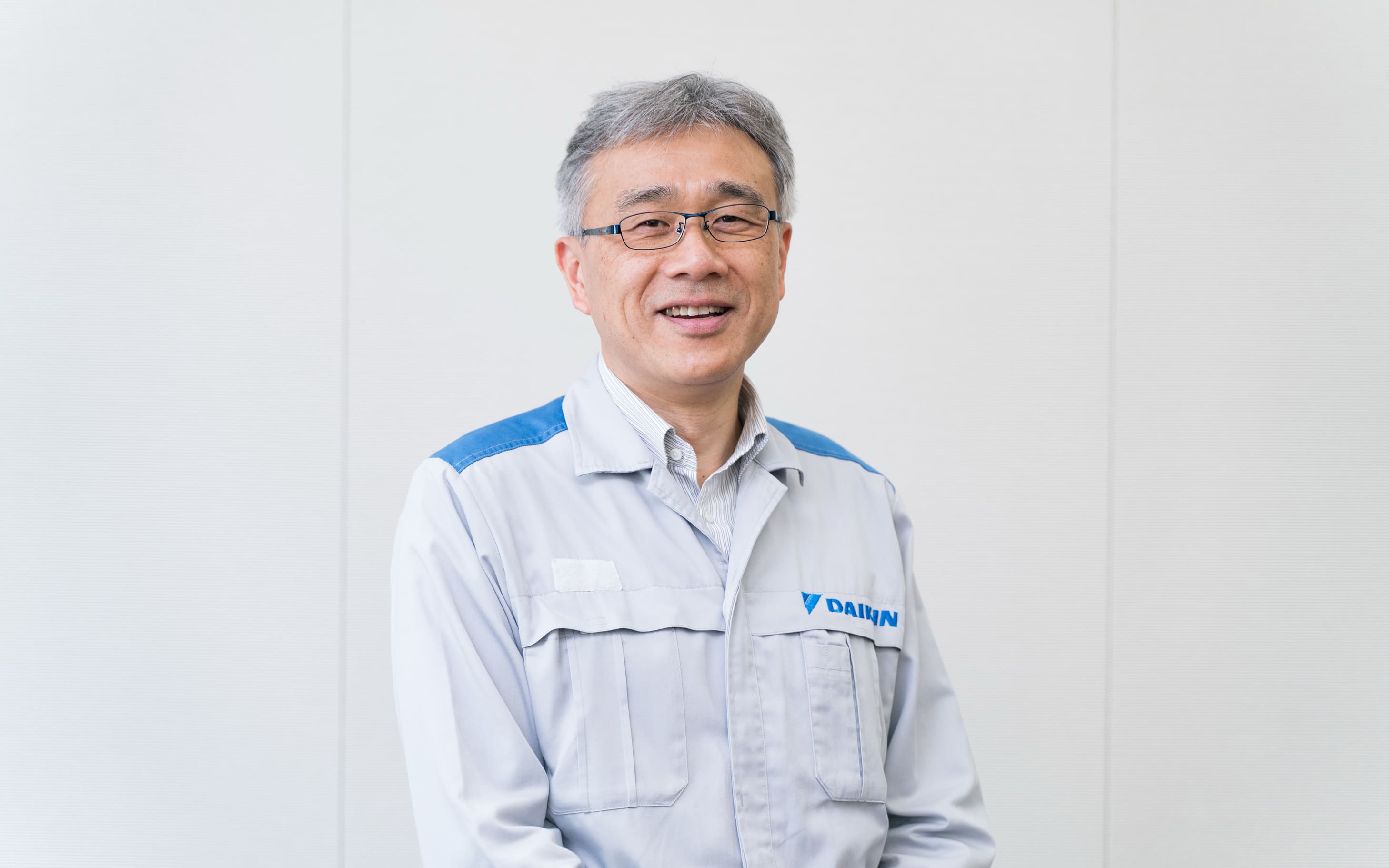
Hideki Matsuura
Chief Engineer, Technology and Innovation Center
Joined the company in April 1993. Born in Osaka.
Aspires to the high goal of becoming the overwhelming No. 1 compressor engineering group in the world.
With pride in our achievements, we continue to take on manufacturing challenges unique to Daikin.
Chief Engineer, Technology and Innovation Center
Joined the company in April 1993. Born in Osaka.
Aspires to the high goal of becoming the overwhelming No. 1 compressor engineering group in the world.
With pride in our achievements, we continue to take on manufacturing challenges unique to Daikin.
Related article